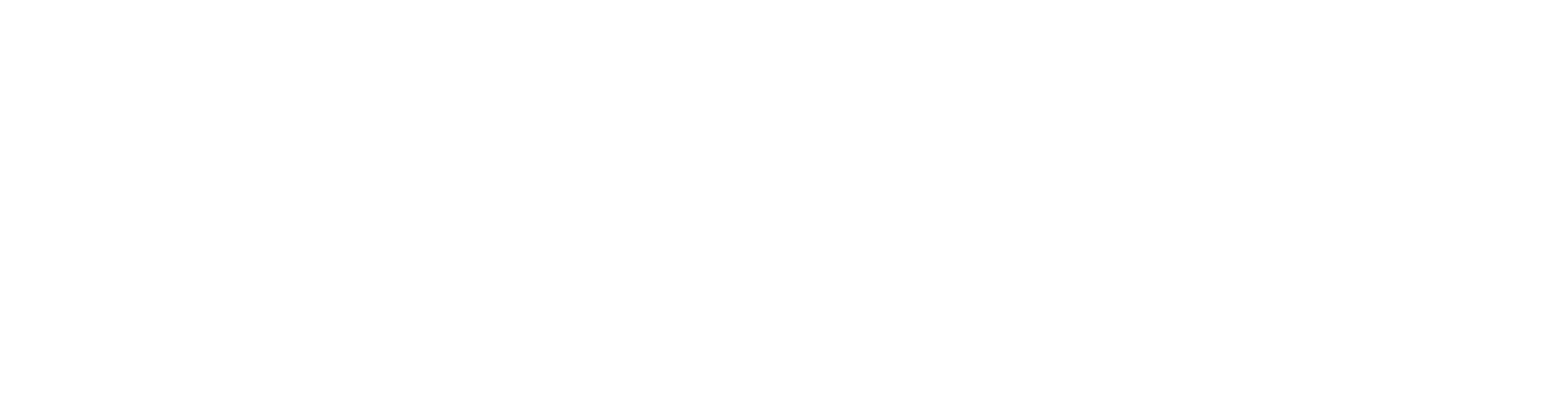
The purpose of the Texas A&M Formula Electric FSAE Team is to develop high-quality engineers who excel in the field of sustainable transportation engineering, primarily through the hands-on design, manufacturing, and testing of an electric formula-style vehicle. I am currently an apprentice engineer for the chassis subteam, and was tasked with developing a sophisticated welding jig system to aid in fabricating a space frame chassis for our AME25' competition vehicle. The design objectives that guided this design involved maintaining tight tolerances to weld a dimensionally accurate frame, creating a manufacturing-friendly design to keep lead times short, and developing an efficient but cost-effective assembly to stay within the project's budget. For this project, I utilized SolidWorks to design and create an engineering solution in manufacturing our team's frame. Engineering justifications for material selections and overall design were derived from simulations, previous-year analyses, and discussions with other subteams.
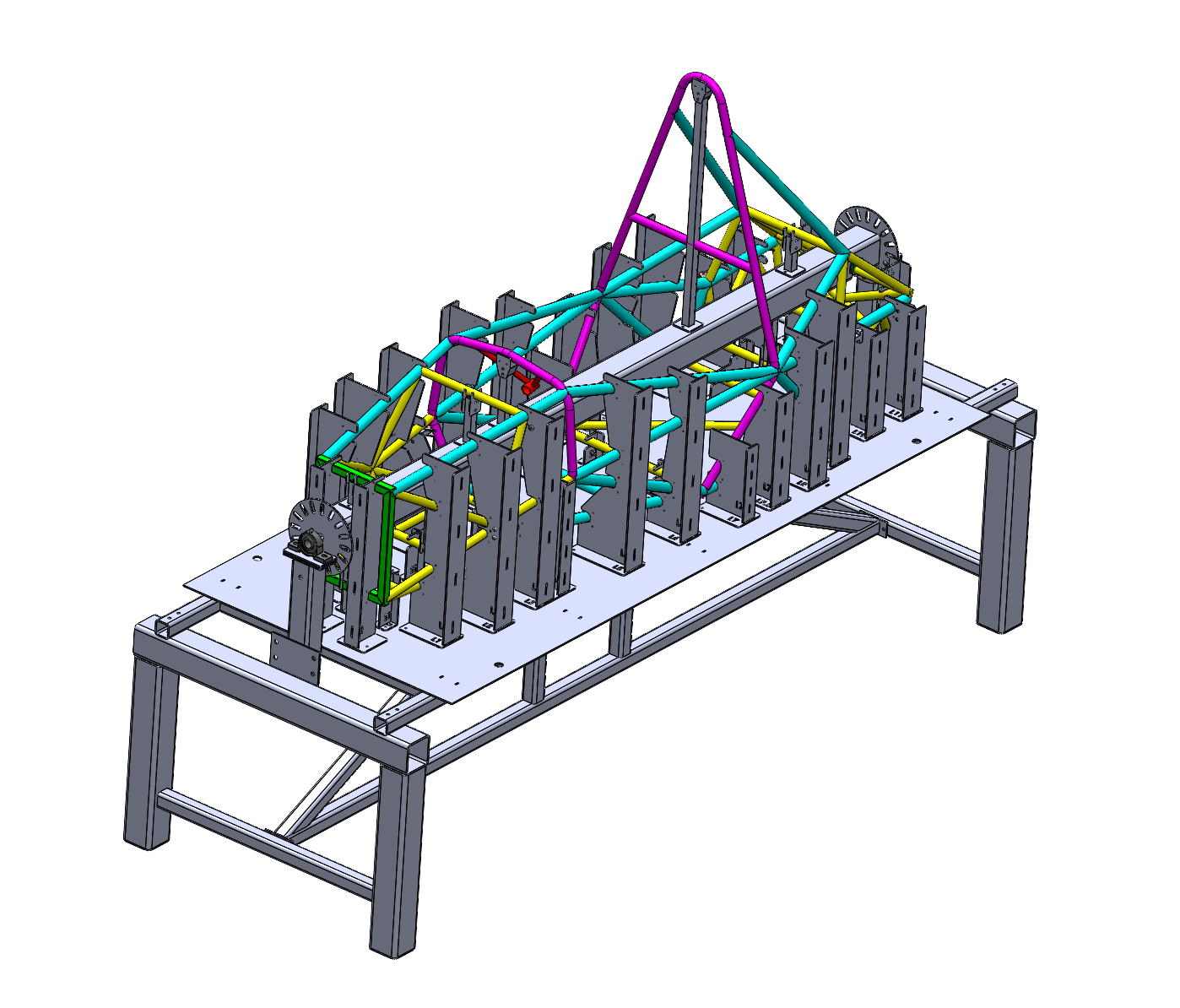
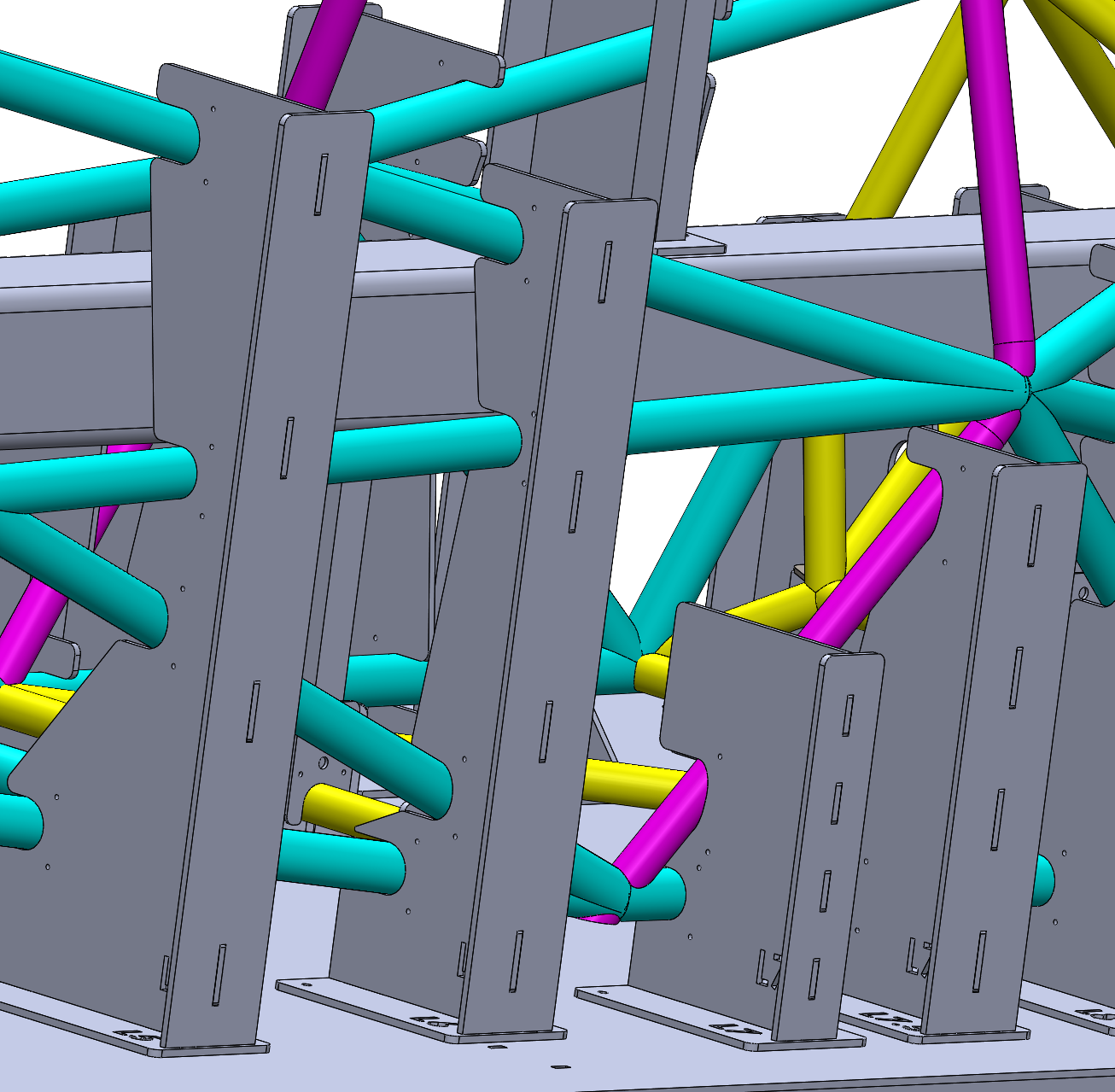
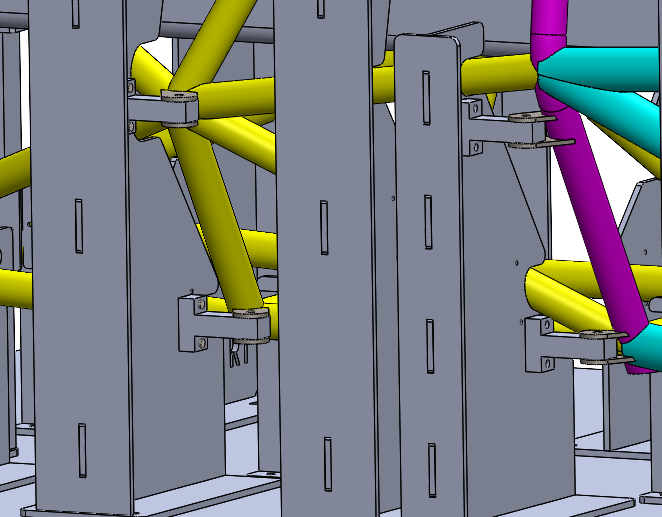
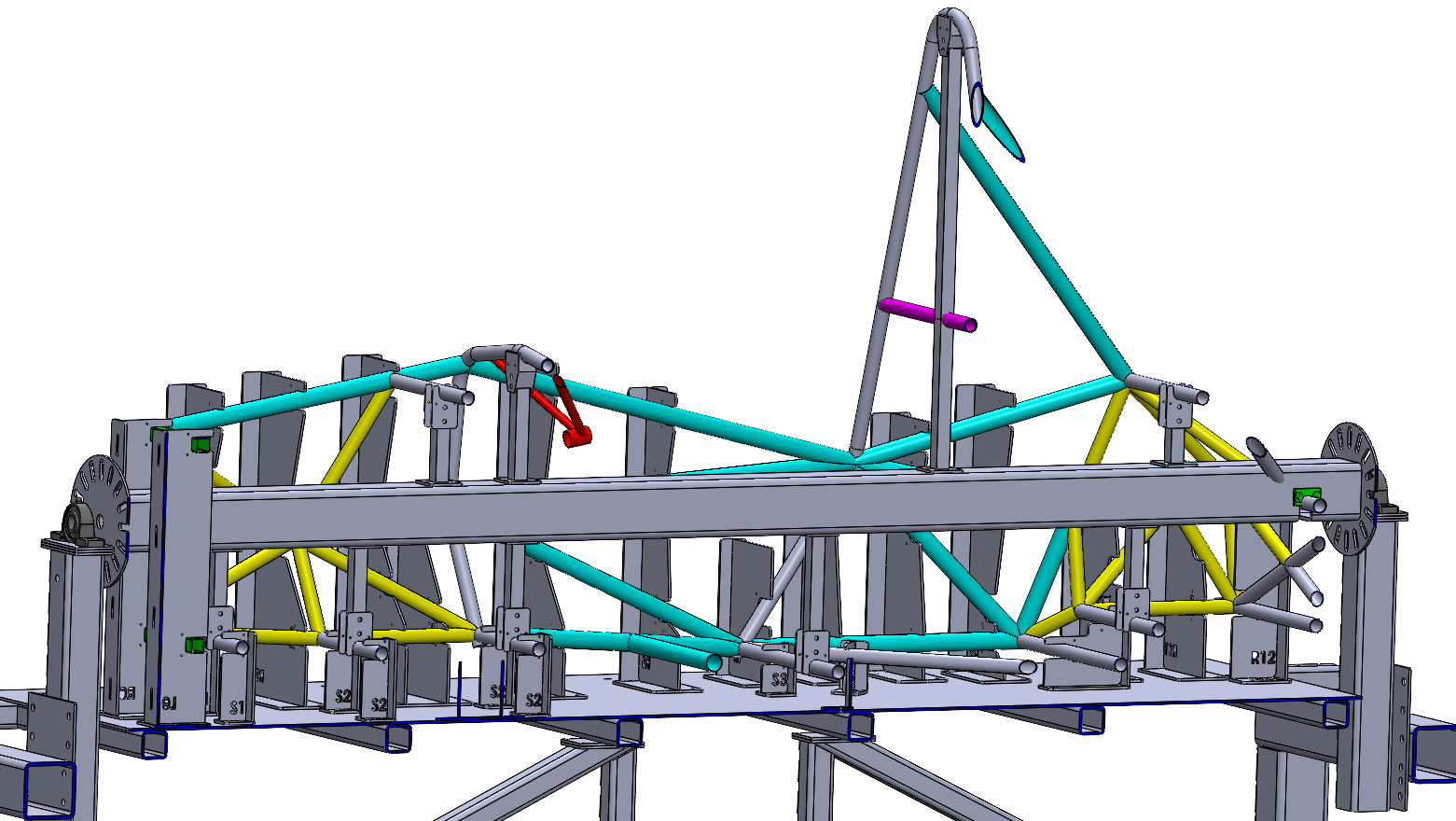
As of January 5th, 2025, all metal parts for the welding jig were received, processed, and inventoried. I am currently in the process of welding together the sheet metal plates and assembling the welding jig. Attached below are pictures displaying my project's progress.
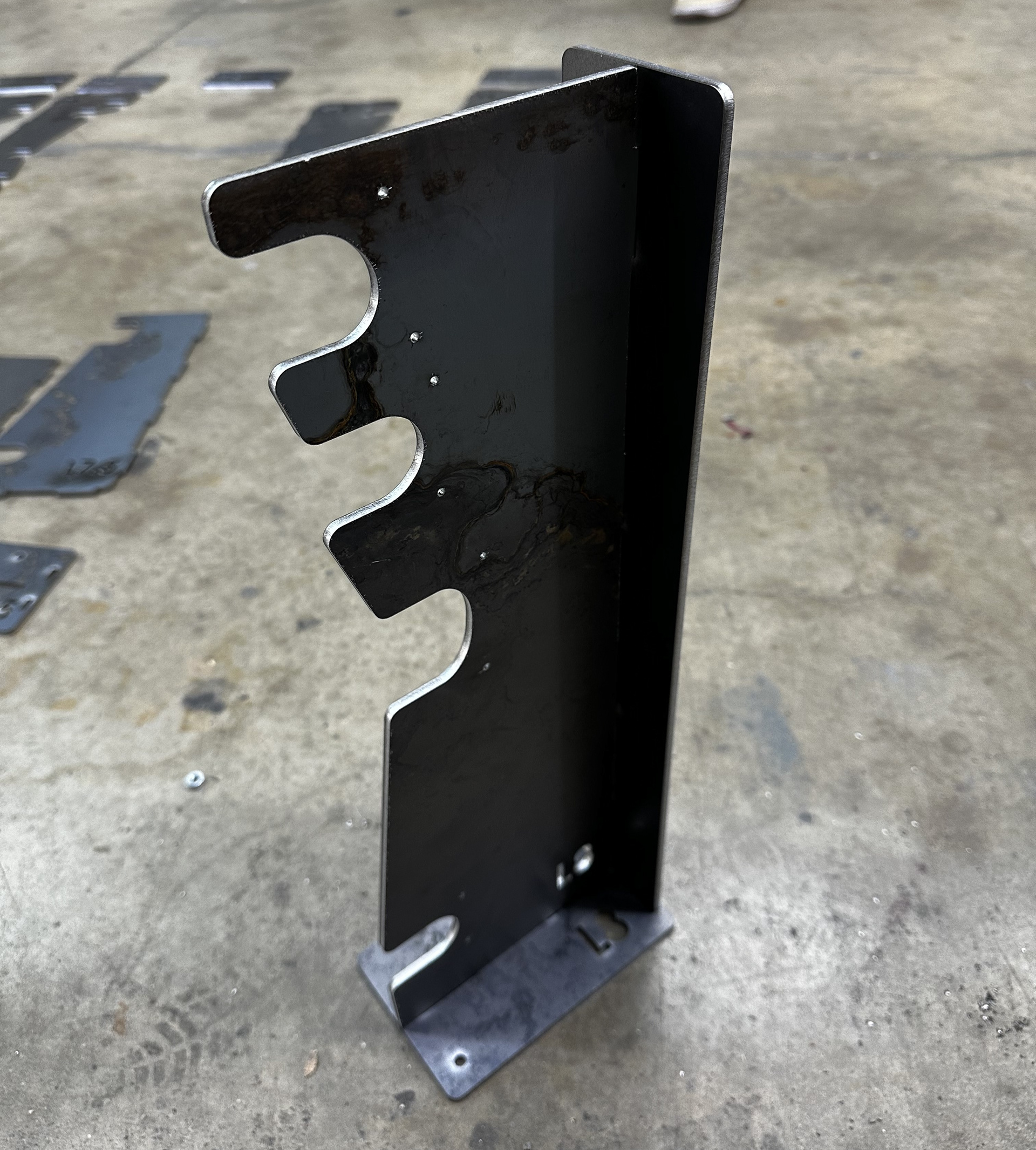
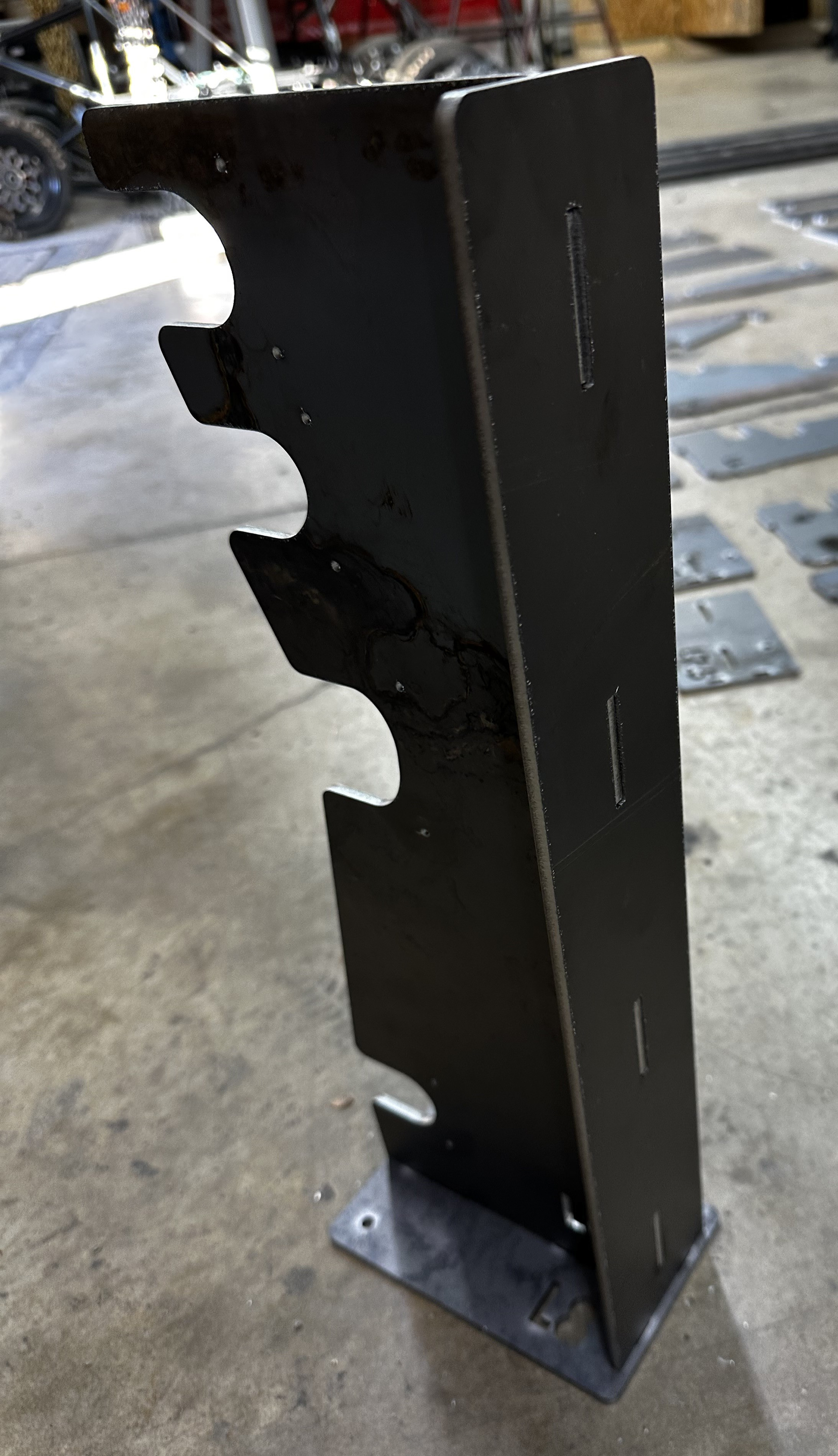
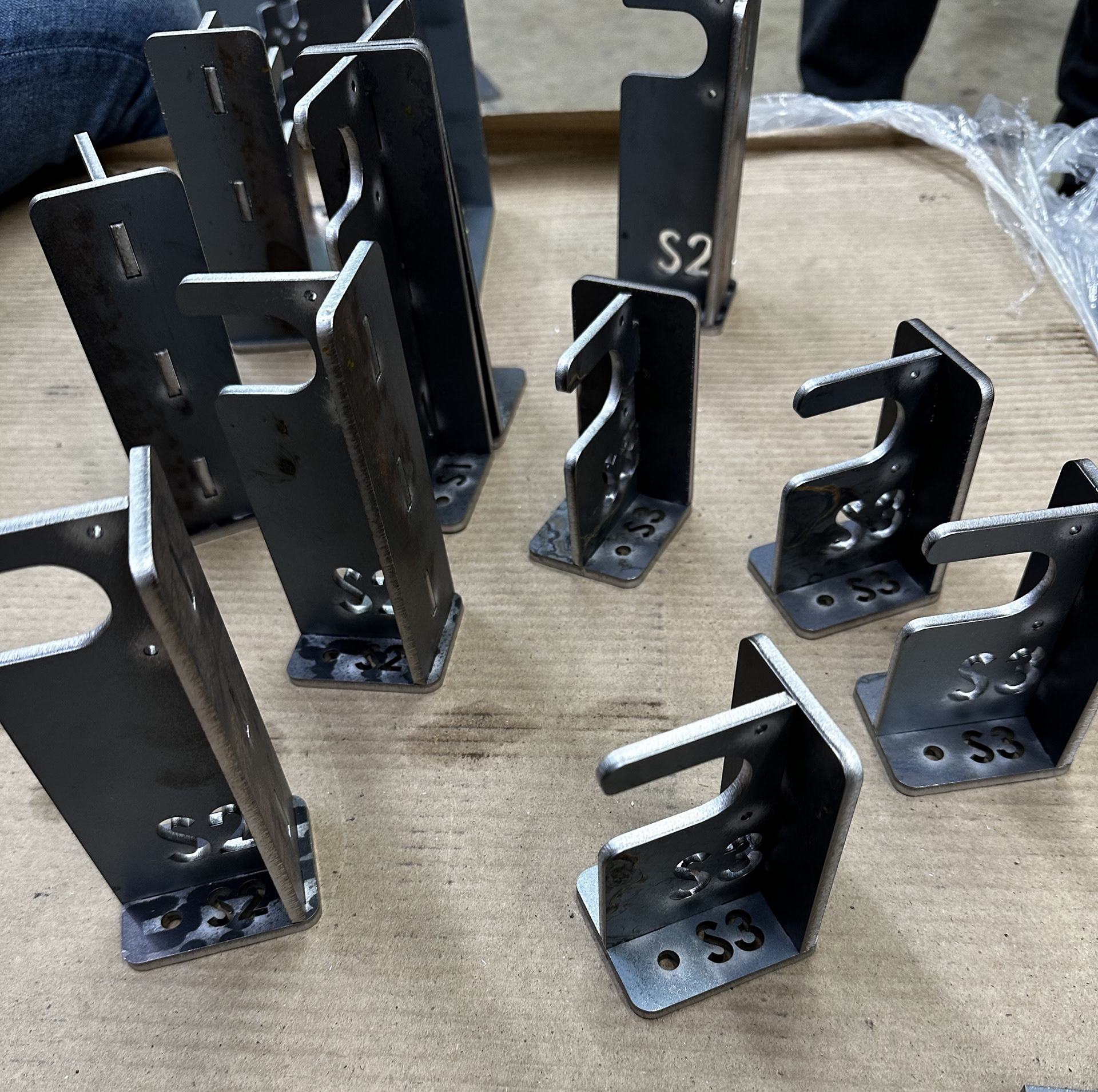
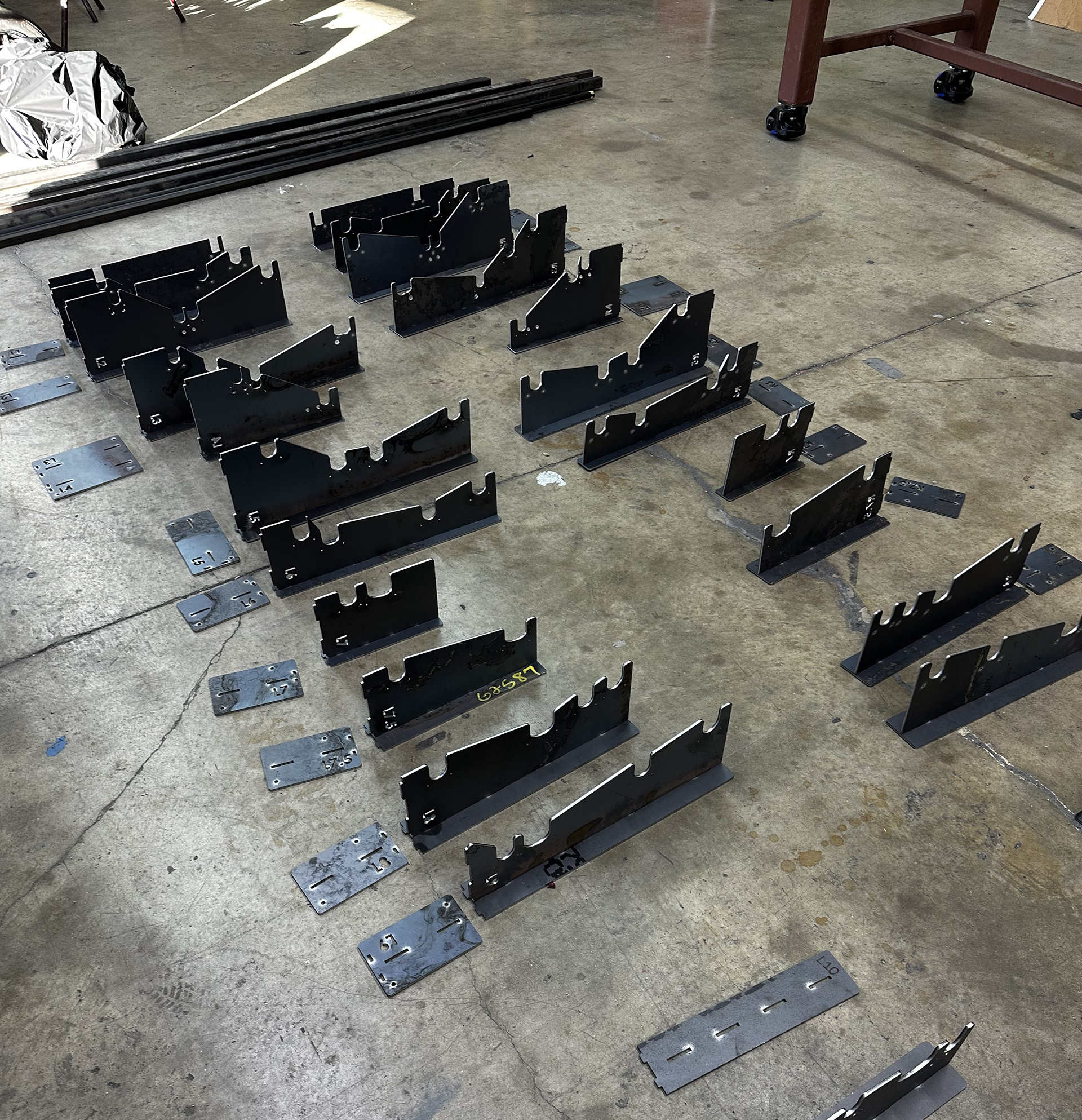
As of January 15, the welding jig was complete with chassis tubes in correct orientation, providing a stable set up to weld the chassis together within the tight tolerances the design required. Fun fact - tubes were measured in the jig, and with minimal error, the real world measurements were 1 to 1 with the dimensions in CAD.
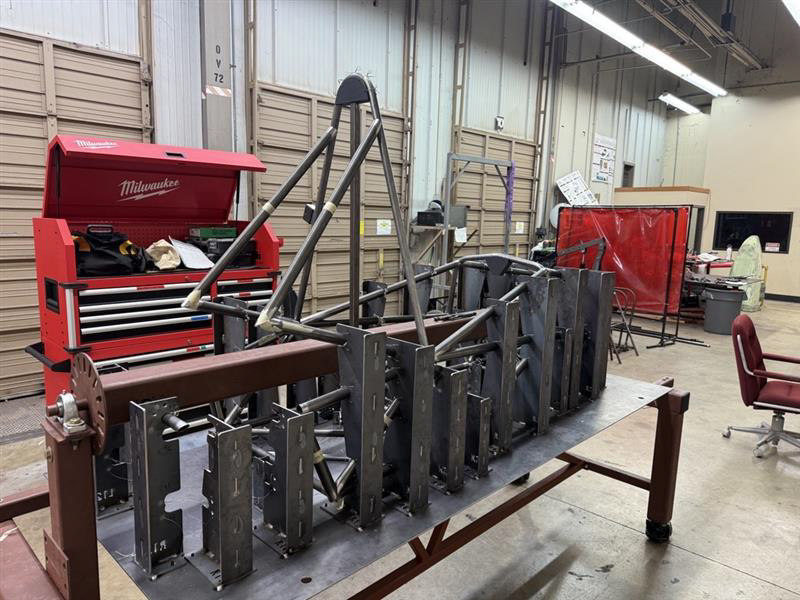

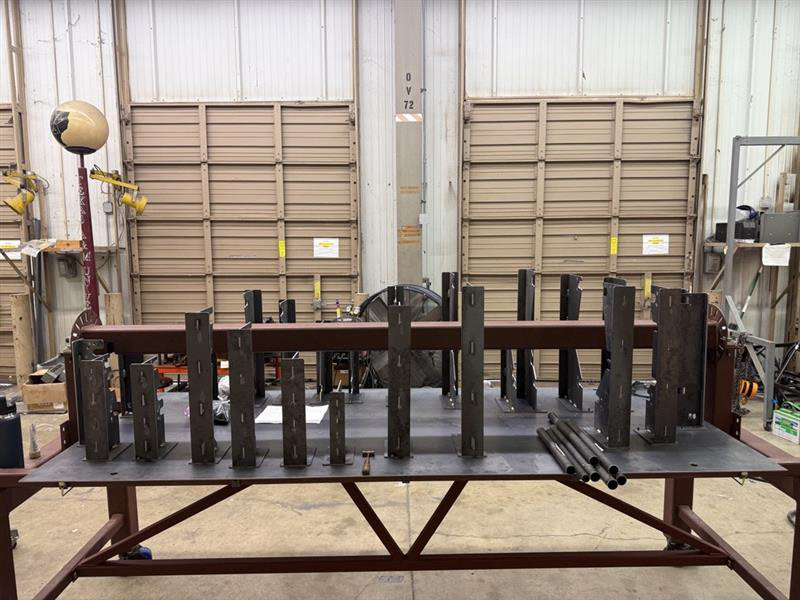
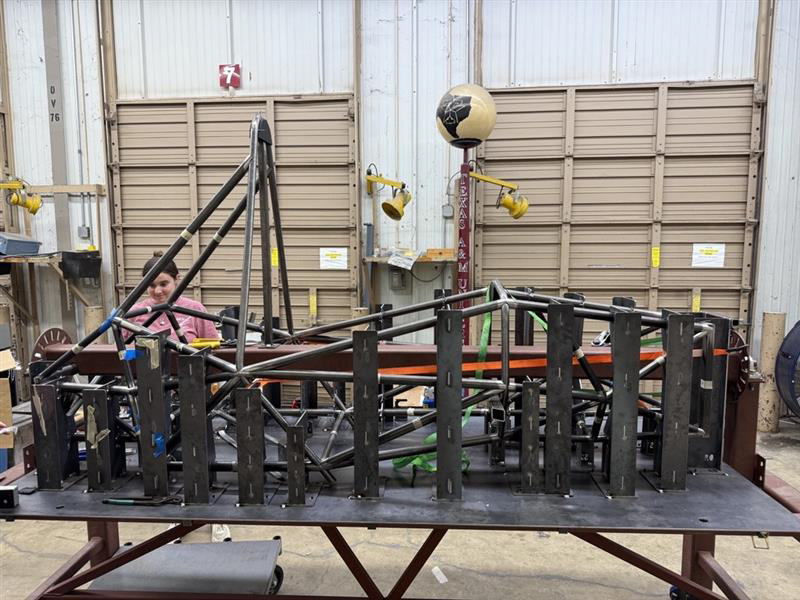